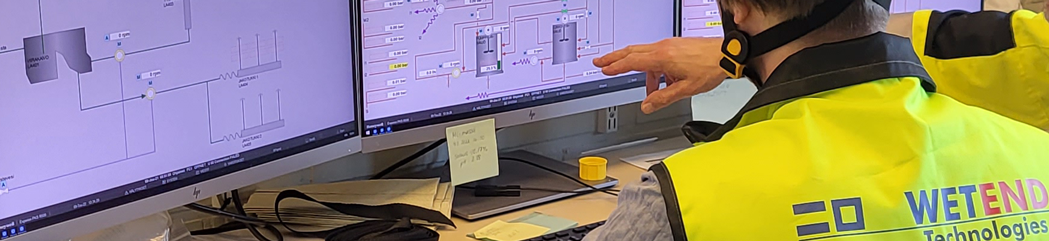
Mixing additives and new raw materials
Trouble-free mixing of MFC and NFC opens new possibilities
TrumpJet Flash Mixing technology fluidizes NFC and MFC and uniformly mixes it into the paper and cardboard pulp in a flash of time. After-screen dosing minimizes additive loss and homogeneous mixing improves product characteristics. Our innovative mixing solutions enable our clients to develop competitive processes and products that meet current challenges and customer demands.
Effective mixing just before headbox for excellent runnability and consistent quality
TrumpJet enables trouble-free mixing of very long and extra-long synthetic or bio-based fibers and prevents the formation of fiber spins, fiber kinks and large fiber flocs, which cause runnability and quality issues. The concept makes it possible to introduce special fiber materials into the process and exploit their benefits by creating new sheet composite structures and characteristics.
Considering chemical mixing optimization?
We can help you to lower production costs, improve machine runnability and product quality, while reducing the environmental impact of your production, and much more.